Introduction
Innovative technologies continue to be adopted by biomanufacturers to meet the ever-increasing demands for higher quality, faster delivery, and lower costs. The use of disposable, single-use production equipment and components is increasing at biopharmaceutical contract manufacturing organizations (CMO) and their clients to improve efficiency, quality and turn-around time. The advantages associated with these technologies in the production of biopharmaceuticals are increasingly evident with the majority of CMOs adopting single-use technologies [1]. Single-use technologies are already widely used for storage and filtration; now they are increasingly being adopted for cell culture, and their use continues to be developed for downstream applications.
While growth rates and market size estimates for single-use systems vary (depending in part on market definitions), most estimates show the market for single-use technologies (both capital and consumables) growing at rates greater than the underlying biopharmaceutical market, reflecting the higher adoption rates of single-use systems. Over the next several years, the market for single-use systems is expected to grow at double-digit rates, with similar growth rates for disposables supporting both upstream and downstream segments of the bioprocess chain.
Increasing Adoption of Disposable Bioreactors in Biomanufacturing
Any new technology in biomanufacturing must offer significant advantages. Since disposable bioreactors were first introduced, users have consistently cited their primary advantages as savings in time, labor, and costs associated with simpler validation and avoidance of the cleaning process [2-4].
Broad adoption of new technologies depends on resolving potential challenges associated with their use in different applications. Biomanufacturers’ perspectives on the barriers to adoption of disposable bioreactors have changed significantly in the last six years.
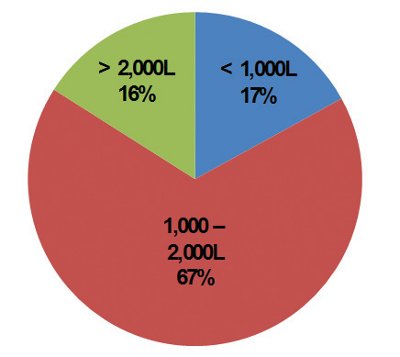
Figure 1 - Feasible Scale of SUB
(HighTech Business Decisions)
When HighTech Business Decisions in 2005 interviewed biomanufacturing directors at biotechnology and pharmaceutical companies worldwide, many viewed disposable bioreactors as a still unproven new technology, and they cited the unavailability of larger scale units as the most significant disadvantage associated with their use. Only 14% of the biomanufacturing directors who were using or planning to use disposable bioreactors in-house or with their CMOs, expected to be doing so at the 1,000L scale by 2008. Accordingly, early adopters of disposable bioreactors used them mainly for earlier stages in production such as seed incoculum and preclinical production [2,3]. By 2009, with the increased availability and experience with larger single-use bioreactors (SUBs), the majority (67%) of the biomanufacturing directors expected a maximum usable SUB volume at 1,000L to 2,000L, while only 17% of the biomanufacturing directors viewed the maximum feasible scale of SUBs to be less than 1,000L (Figure 1) [4].
The trend towards ever larger single-use bioreactor scale seems reasonable, with 16% of the biomanufacturing directors expecting SUB usable volume greater than 2,000L. However, the two trends of a) biologic drugs targeting smaller patient populations, and b) higher expression titers may obviate the need for SUB usable volumes matching large scale stainless steel bioreactors. While limitations and other concerns persist about the use of SUBs (e.g., leachables and extractables, cost of consumables, environmental impact of bag disposal), these concerns are not at levels sufficient to prevent their increasing adoption. In 2005, 44% of the biomanufacturing directors that HighTech Business Decisions interviewed were using disposable bioreactors. By 2007, that number grew to 59% [3], an increase of 15 percentage points.
CMOs Expand Use of Disposable Bioreactors to Meet Client Needs
A recent survey of CMOs by HighTech Business Decisions shows that most CMOs continue to expand capacity in response to anticipated market growth. In selecting bioreactors, most CMOs are adding single-use bioreactor capacity. Disposable bioreactors have become increasingly accepted for early stage production as well as for production of clinical phase biopharmaceuticals. CMOs have invested in single-use bioreactors to meet the demands for flexible, small batch processing that is typical of early phase clinical production.
Ralph Lambalot, Divisional Vice President, Biologics Development & Manufacturing Launch at Abbott, describes his company’s example. “Abbott recently upgraded a production suite to use entirely single-use cell culture and purification equipment. Benefits of this addition address the ever-growing market demands for faster and lower cost early phase production.”
Just weeks after FUJIFILM Corporation acquired the Merck BioManufacturing Network, the CMO now known as Fujifilm Diosynth Biotechnologies announced its latest step in an ongoing project to boost its cell culture capacity. Complementing the existing 200L SUB at its Cary, North Carolina site, the company added single-use mixers, single-use harvest filtration and a 1,000L single-use bioreactor to its RTP site as well. Designed for variable volume operation ranging from 200L to 1,000L, the unit offers the advantage of flexibility to the CMO. “The flexibility of scale will allow us to better serve the demands of companies requiring material for pre-clinical studies, early to mid-phase clinical production and beyond,” said John Foy, Vice President of Business Development and Logistics.
Although first adopted for early stage, smaller scale production, disposable bioreactors have now advanced in scale and operation to the point where a number of CMOs have recently begun using larger disposable stirred tank bioreactors for commercial production.
Joe McMahon, President and CEO at KBI Biopharma, reports that his company recently added cGMP mammalian cell culture capacity in the form of bioreactors (up to 2,000L). The line is designed for both clinical and commercial production and utilizes single-use technology.
CMC Biologics has expanded its larger single-use capacity at both its Bothell, Washington and Copenhagen sites. “The expansion plans started with the construction of a multi-purpose single-use facility, which was completed in 2010, and is expected to include the build-out of a facility to house two 5,000L commercial-ready manufacturing lines,” notes CEO Claes Glassell. Mr. Glassell reports that CMC also plans to add a 2,000L SUB to its Copenhagen facility by the end of 2011.
Adoption of larger scale disposable bioreactors offers advantages to both CMOs and their customers. Wieland W. Wolf, PhD, CEO of ProBioGen notes that single-use bioreactors at larger scale will allow his company to serve its clients from clinical phases through commercialization, which benefits both the client and the CMO. “The adoption of larger scale SUBs reduces project timelines and eliminates the technology transfer for clients requiring larger volumes as they move to late phase and commercial production.” Dr. Wolf also notes the benefits of single-use bioreactors at ProBioGen, “On our side, we will benefit from the reduced timelines in connection with getting a SUB-based facility up and running compared to conventional stainless steel bioreactors, and we also benefit by avoiding costly cleaning validations in change-over procedures.”
CMO Pricing Expectations Using Disposables
One of the benefits often cited in the use of large-scale, single-use bioreactors is lower production costs compared to stainless steel bioreactors. The lower costs result from lower upfront costs and higher capacity utilization rates. Reduced upfront costs consist of lower capital expenditures for equipment, factory utilities, and lower qualification costs. The lower costs associated with ongoing production include greater flexibility, lower labor costs, and higher production utilization rates.
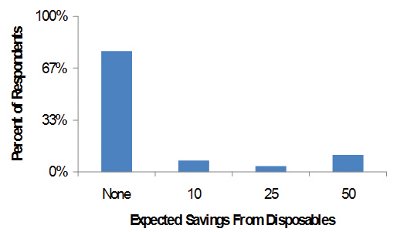
Figure 2 - Expected CMO Savings
(HighTech Business Decisions)
In HighTech Business Decisions latest report, Biopharmaceutical Contract Manufacturing: Best Practices Pricing Study 2011 [5], biomanufacturing directors from biotechnology and pharmaceutical companies discussed their batch price expectations from a CMO using single-use bioreactors versus using stainless steel bioreactors to produce their biologic. Over two-thirds of the biomanufacturing directors expect to pay the same batch price without regard to the type of bioreactor used. While less than one-third of the biomanufacturing directors expect 10% to 50% lower prices from a CMO using single-use bioreactors (Figure 2). A few biomanufacturing directors report that they expect the higher productivity achieved from their CMOs’ using single-use bioreactors would be offset by higher pass-through cost associated with the purchase of consumables.
A further analysis of the responses shows different price expectations between biomanufacturing directors in North America versus biomanufacturing directors in Europe and ROW. Only 17% of the Europe and ROW biomanufacturing directors expect different prices from their CMOs that use single-use versus stainless steel bioreactors compared to 40% of the North American biomanufacturing directors. Thus North American biomanufacturing directors are more than twice as likely to expect lower prices from their CMOs who use single-use bioreactors compared to biomanufacturing directors located in Europe and ROW. The different price expectations between biomanufacturing directors in different world areas may result from a) the higher relative labor costs in North America compared to other world areas, b) a business and legal environment that makes it easier for US-based operations to take advantage of these productivity gains, or c) consumable prices related to disposables may be included in batch pricing assumptions.
In low-cost regions of the world, the labor savings associated with the use of disposables may not justify the higher cost of consumables. Similarly, employment laws and customs in certain regions may make it difficult to reassign or reduce employment levels in order to take advantage of higher productivity levels. Moreover, depending on a CMO’s project backlog, higher productivity may result in greater idle capacity; thereby, offering no net economic benefits in the short run. In addition, many CMOs employ a combination of stainless steel and single-use technologies, thus making specific price adjustments for specific processes difficult to determine. This is especially true when factory indirect costs are shared between different processes. Finally, most CMOs’ service offerings include more than just direct production services; thus there are many factors that determine project pricing, and direct cost of manufacture is just one factor that plays a role in overall CMO pricing.
Use of Disposables in Other Functional Areas
Disposable technologies are not only being employed in biologic manufacturing, but it is also being employed in ancillary production functions and laboratories. For example, EMD Millipore has recently introduced a bioreactor with a standard stirred-tank format for use in development and optimization of cell culture processes; it is designed to replace traditional benchtop glass bioreactors and reduce the turnaround time associated with their cleaning, assembly and sterilization. According to Mani Krishnan, Director, Single-Use Processing Systems, “New features include an injection port for small volume additions, a sub-surface fluid port for either addition or removal, and an additional port for insertion of a third probe.” Krishnan further explains, “Enhanced operational and process monitoring capabilities benefit process development scientists by enabling operations such as perfusion and monitoring of additional cell culture parameters such as carbon dioxide, viable cell density, or optical density.”
Concluding Remarks
Biopharmaceutical contract manufacturers continue to invest in disposable technologies to increase manufacturing efficiencies. Single-use products and systems are used effectively for filtration and biocontainment of buffers and media. Starting with small-scale production, disposable technologies have become an important option for some applications in larger scale manufacturing, and it will continue to foster improvements in other areas. Acceptance and integration of single-use bioreactors have widened in recent years, and single-use disposable systems are increasingly being used by biopharmaceutical contract manufacturing organizations.
References
- Ott, KD. 2011. Are Single-Use Technologies Changing the Game? BioProcess Int. 9:S48-51
- Biopharmaceutical Contract Manufacturing 2005: Improved Processes and New Capacity for Pipeline to Commercial Production. HighTech Business Decisions, San Jose, CA. Available from: http://www.hightechdecisions.com/.
- Biopharmaceutical Contract Manufacturing 2007: Quality, Capacities and Emerging Technologies. HighTech Business Decisions, San Jose, CA. Available from: http://www.hightechdecisions.com/.
- Biopharmaceutical Contract Manufacturing 2009: Expanding Markets, New Capacities and Improved Performance. HighTech Business Decisions, San Jose, CA. Available from: http://www.hightechdecisions.com/.
- Biopharmaceutical Contract Manufacturing: Best Practices Pricing Study 2011. HighTech Business Decisions, San Jose, CA. Available from: http://www.hightechdecisions.com/.
Author Biographies
William Downey is president, and Helen Nicely, Ph.D. is a senior research analyst at HighTech Business Decisions.
www.hightechdecisions.com
[email protected].
Phone: 408-978-1035.
This article was printed in the July/August 2011 issue of American Pharmaceutical Review - Volume 14, Issue 5. Copyright rests with the publisher. For more information about American Pharmaceutical Review and to read similar articles, visit www.americanpharmaceuticalreview.com and subscribe for free.